第一次使用氧化物和碳的復合耐火材料是在15世紀初所制造的碳一氧化物坩堝。煉鋼工業(yè)使用碳一氧化物復合耐火材料的例子則是很早作為鑄錠用耐火材料的石墨塞頭磚。后來,隨著連鑄的推廣應用,廣泛使用的滑板、水口磚、浸入式水口磚等也都是由氧化物(主要是Al2O3)和碳復合起來的耐火材料。轉爐煉鋼的初期,采用不燒成的焦油/瀝青結合的自云石磚則是在100年以前就已開發(fā)出來的含碳耐火材料。但這種耐火材料由于耐用性有限度,以及為了提高耐磨性和抗氧化性而逐步向燒成磚過渡,即使用了焦油/瀝青浸漬的燒成磚??梢哉f,這種轉爐襯磚是一種剛好含有足夠的碳充填氣孔結構的鎂磚或者鎂白云石磚。由于這些耐火材料中焦油/瀝青在使用時發(fā)生了碳化作用(磚中殘?zhí)剂考s為%),對于提高轉爐工作襯用MgO—CaO系列耐火材料的使用性能發(fā)揮了重要的作用。所有這些含碳耐火材料,實際上都是我們今天煉鋼爐上采用的MgO—C磚和MgO—CaO—C磚的前驅。
為了提高焦油/瀝青結合耐火材料中的殘?zhí)剂?/SPAN>(達到約5%C),一些國家曾經(jīng)采用添加炭黑的辦法,以增加耐火材料中的固定炭。不過,碳含量超過5%時,碳就不只是充填氣孔結構而是一種對耐火材料的許多性能起到主導作用的組分。所以,當含碳耐火材料中配入8%—10%以上的多量碳時,則稱之為氧化物一系復合耐火材料,其中MgO—C磚則是日本首先開發(fā)的耐火產(chǎn)品。
日本當時研制MgO-C磚是作為電爐應用而開發(fā)的,于年在電爐上開始了實用性試驗,通過六年的試驗研究工作之后被正式推廣應用。過了兩年,他們又將MgO—C磚應用到盛鋼桶和鐵爐,其轉爐爐底及風口選用樹脂結合不燒成的MgO—C(石墨)系耐火材料,取得了巨大成功,從而開創(chuàng)了含石墨的復合耐火材料在轉爐上應用的先例。
在日本人研究使用合成樹脂結合的MgO—C磚之后,西歐則開發(fā)r瀝青結臺的MgO—C磚,其殘?zhí)剂考s為10%。這一研究則是基于傳統(tǒng)的瀝青結合對耐火材料很可靠。由于價格低于合成樹脂結合的MgO—C磚,所以這些瀝青結合的MgO—C磚被成功地用于水冷電爐中的高溫熱點以外的部位,同時也用于轉爐。
MgO—C磚在結合方式、碳含量和碳的類型上都不同于常用的含碳耐火材料。最早的MgO—C磚碳含量將近8%,現(xiàn)在已遠遠超過這一數(shù)量。通常,MgO—C磚主要是在鎂砂和鱗片狀石墨中作為結合劑添加了熱硬化性樹脂,加入或不加入防氧化劑的不燒磚。它是依據(jù)碳具有熔點非常高,難于被鋼水和鋼渣濕潤;熱傳導率高,難于受熱沖擊而產(chǎn)生裂紋以及還可以還原Fe2O3和SiO2等外來物的優(yōu)點。雖然具有容易被氧化的缺點,但通過碳與MgO復合可使碳的氧化得到抑制,同時也克服了鎂砂(MgO)的缺點——由于熱沖擊而產(chǎn)生裂紋,由于外來物成分的侵入而產(chǎn)生結構剝落,所制造的具有C和MgO各自優(yōu)點并克服了二者的缺點的MgO和復合的耐火材料,從而發(fā)揮出優(yōu)良性能。也就是說,MgO~C磚完全克服了過去堿性耐火材料的缺點,即爐渣侵蝕和發(fā)生裂紋的致命問題。
由于MgO-C系耐火材料100%地利用了天然石墨(鱗片)、難于與熔渣潤濕、熱導率高以及應力緩和能力大等特性,最大限度地發(fā)揮了MgO的高耐蝕性能,因而這類耐火材料是劃時代的耐火材料。
MgO—C磚發(fā)展的基礎是結合劑技術。從探討與碳的親和性、粘性、強度、殘?zhí)剂康确矫婵?,有分開使用或同時使用了酚醛樹脂的。對于MgO—C磚來說,第一個決定性的技術步驟是石墨用于MgO—C磚的生產(chǎn)中,第二個決定性的技術步驟則是采用合成樹脂作為牛產(chǎn)MgO—C系復合耐火材料的結合劑,從而在技術上能夠生產(chǎn)出碳含量大大增加(多于20%的c)的MgO—C磚。這是Mgo—C磚能迅速發(fā)展的一個重要前提。
80年代初期,在煉鋼爐上使用的MgO—C磚不含防氧化劑,稱為第一代產(chǎn)品。第二代產(chǎn)品含有防氧化劑,研究第二代產(chǎn)品的目的在于保護碳盡可能長時間不被燒掉,以及阻滯MgO和C的高溫反應。
相關資訊
27
2024-04
02
2023-09
22
2023-08
22
2023-08
23
2022-11
16
2022-07
13
2022-07
11
2022-06
30
2022-05
熱門產(chǎn)品
全國咨詢熱線
13608687008
鄭州新密市超化鎮(zhèn)工業(yè)園區(qū)
備案號:豫ICP備16041729號
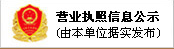