我國生產(chǎn)的高鋁磚,大都采用鋁礬土熟料;再配合一定數(shù)量的結(jié)合粘土而制得。煅燒高鋁礬土熟料多采用回轉(zhuǎn)窯或豎窯;而煅燒高鋁磚多采用隧道窯或倒焰窯。
在以粉煤、柴油或重油為燃料的回轉(zhuǎn)窯內(nèi)蝦燒高鋁礬土熟料時。應(yīng)以低的能源消耗、高的作業(yè)率燒制出合乎要求的熟料。為此,要根據(jù)物料在高溫下的物理變化特征來制訂一個合理的煅燒制度,在制訂煅燒制度時,高鋁礬土熟料煅燒中的幾個問題要注意。
1.物料的塊度
進(jìn)入回轉(zhuǎn)窯的物料塊度的確定,要以原料特點(diǎn)為依據(jù)。如果物料中TiO2或K2O、Na2O含量較高,易于燒結(jié),物料塊度可以放大,但最大塊度不超過40mm。物料經(jīng)篩分后分為8~40mm(及<8mm兩種。首先加入<8mm的小料塊,待燒成帶的內(nèi)襯耐火磚掛上窯皮后,再加入8~40mm的大塊料。如此循環(huán)加料,既保護(hù)了窯襯,又避免了結(jié)圈現(xiàn)象。如果物料中K2O、Na2O等雜質(zhì)成分含量較少,可選用較小的塊度,最大塊度以不超過20mm為宜。
2.窯尾溫度
窯尾溫度也要根據(jù)物料的特性而定。如果物料為D~K型礬土,在400~600℃下,水鋁石脫水變成剛玉假相;高嶺石變?yōu)闊o永高嶺石。因此,在脫水階段窯溫不得高于400℃。如果物料入窯后,窯尾溫度突然高于該溫度,物料本身就會自行爆裂,形成較多的細(xì)小顆粒,因而促使結(jié)圈現(xiàn)象的發(fā)生;如果窯尾溫度過高,勢必使高溫區(qū)移向窯尾一端,產(chǎn)生的結(jié)圈亦后移。處理結(jié)圈,勢必影響回轉(zhuǎn)窯的作業(yè)率。而且,窯尾溫度過高,帶走的余熱多,增加燃料消耗。因此,窯尾溫度以控制在220~400℃為宜。
3.煅燒溫度
高鋁礬土的燒結(jié)溫度與礬土中雜質(zhì)氧化物的種類和數(shù)量有關(guān)。其中,對燒結(jié)溫度影響最大的是R2O。當(dāng)R2O含量在3.0%以內(nèi)時,其燒結(jié)溫度與R2O含量間的經(jīng)驗關(guān)系式為:
t=1625~91.4R
式中t--燒結(jié)溫度,℃;
R--R2O含量,%。
對于泥狀結(jié)構(gòu)及粒狀結(jié)構(gòu)的高鋁礬土,其物料的燒結(jié)溫度分別比經(jīng)驗關(guān)系式計算出的溫度降低或升高10~20℃。煅燒溫度低,物料欠燒;煅燒溫度高,大量生成玻璃相,都達(dá)不到所要求的體積密度和氣孔率指標(biāo)。
同樣,Fe2O3、CaO也影響高鋁礬土的燒結(jié)溫度,只不過比R2O的影響小得多。
高鋁礬土的燒結(jié)溫度主要取決于Al2O3/SiO2比值為2。Al2O3/SiO2比值為2.55的Ⅱ等高鋁礬土難于燒結(jié),其燒結(jié)溫度為1700℃。特等和I等高鋁礬土的燒結(jié)溫度為1550~1600℃,Ⅲ等高鋁礬土在1500℃左右便可燒結(jié)。
4.煅燒時間
物料莊回轉(zhuǎn)窯內(nèi)的停留時間與礦石的入料量有關(guān),而入料量又取決于轉(zhuǎn)速。因此,調(diào)節(jié)回轉(zhuǎn)窯的轉(zhuǎn)速可控制物料的煅燒時間。物料在窯內(nèi)的停留時間r、窯的內(nèi)徑d、長度L、斜度S、轉(zhuǎn)速n有如下的關(guān)系:
r=
由于回轉(zhuǎn)窯的窯型選定后,上述參數(shù)基本固定,唯有轉(zhuǎn)速能影響物料在窯內(nèi)的停留時間。所以,除了正確地選擇窯型外,還必須考慮窯的最佳轉(zhuǎn)速,保證物料有足夠的煅燒時間,以使物料達(dá)到燒結(jié)。回轉(zhuǎn)窯的轉(zhuǎn)速、下料量與物料的煅燒時間有如下的參數(shù)關(guān)系。當(dāng)轉(zhuǎn)速為58~60r/min,下料量為1500~
5.火焰性質(zhì)
在回轉(zhuǎn)窯中煅燒高鋁礬土應(yīng)采取什么性質(zhì)的火焰,是一個有爭議的問題。實踐表明:采用還原焰煅燒,體積密度較低,物料斷面易產(chǎn)生細(xì)小裂紋。這種情況,一是因為還原焰的燃燒溫度易受過??諝庀禂?shù)的影響,因而燃燒不穩(wěn)定;二是因為物料中的氧化物在缺氧情況下,具有放氧作用,從而影響物料的燒結(jié)。因此,煅燒高鋁礬土最好采用弱氧化性火焰。弱氧化焰可以使火焰具有了7~9m的長度,因而燃燒溫度穩(wěn)定,獲得的礬土熟料體積密度高、波動小,礬土熟料的質(zhì)量較穩(wěn)定。
6.窯體冷卻
為了降低窯體表面溫度,不少廠礦在筒體表面閑水冷卻。在實際運(yùn)行中發(fā)現(xiàn),由于水冷,窯內(nèi)砌筑的高鋁磚剝落,掉頭現(xiàn)象嚴(yán)重。當(dāng)停止水冷卻時,砌筑高鋁磚剝落現(xiàn)象明顯減少。此外,水冷卻會加速窯爐外殼鐵皮的氧化,因此,窯皮水冷不如風(fēng)冷好。
7.物料的冷卻速度
實踐表明:不同的冷卻速度對熟料的體積密度有一定的影響。在同樣的煅燒溫度下,當(dāng)熟料進(jìn)入冷卻簡立即水淬冷卻時,熟料顏色變?yōu)榛仪嗌?,體積密度低;但通過冷卻簡全程冷卻后,其體積密度比水淬者高0.02~0,
8.燃料與燒嘴的選擇
根據(jù)當(dāng)?shù)厝剂腺Y源的不同,可選用粉煤、柴油或重油作為回轉(zhuǎn)窯煅燒礬土熟料的燃料。
9.改進(jìn)回轉(zhuǎn)窯煅燒高鋁礬土質(zhì)量的措施
我國高鋁礬土原料多屬D~K型。但是,由于原料中R2O、TiO2含量較高、波動大、采用塊狀原料的煅燒工藝流程,因此礬土熟料質(zhì)量不如圭亞那。蘇里南等國;出口價格也比這些國家同類產(chǎn)品的價格低40~60%。為改變這種狀況,在現(xiàn)有回轉(zhuǎn)窯煅燒礬土熟料技術(shù)的基礎(chǔ)上,應(yīng)采取以下改造措施:
1)進(jìn)窯的原料應(yīng)采取礦石均化成球工藝
我國高鋁礬土原料既有致密塊狀料,又有不均勻的疏松粒狀料。采用原決煅燒熟料很不容易達(dá)到燒結(jié)要求。從成分上看。即使是同一礦區(qū)的原料。成分變化也是較大的。因此,礦石在人窯前要經(jīng)過均勻化處理:進(jìn)行磨細(xì)、配比、壓球作業(yè)。這樣,不僅可以利用粉礦并制成不同等級的熟料,減小批量產(chǎn)品質(zhì)量的波動,而且也有利于降低熟料的燒成溫度。
2)采用原料提純、合成煅燒工藝
由于我國高鋁礬土礦石中TiO2、Fe2O3、R2O含量較高,因此礬土熟料中的玻璃相、剛玉相含量高,莫來石相含量低。為了改善高鋁磚的高溫性能,就需要增加礬土熟料中莫來石相的含量,減少玻璃相含量。為此,如果將高鋁礬土原料經(jīng)過浮選、提純,去掉有害的雜質(zhì)氧化物;按照原料的化學(xué)礦物組成再配人一定量的粘土,以增加燒后莫來石相的含量,則這樣的礬土熟料質(zhì)量可與圭亞那的礬土熟料相媲美。
10.用豎窯煅燒高鋁礬土熟料
以較純的高鋁礬土為原料,在豎窯中掌握適當(dāng)?shù)撵褵郎囟仁顷P(guān)鍵,再加上采用合理的煅燒工藝條件和正確的操作,可以煅燒出品質(zhì)較好的高鋁礬土熟料。
1)煤與礦石的比例為1:8~l:10。
煅燒每公斤礦石的熱耗為2500~3100kJ。
每層礦石的加入量為1500~
2)裝窯每三層作為一個循環(huán)
層次數(shù)量、層位高低、煤比變化,均應(yīng)根據(jù)底火實際情況加以控制。
3)通風(fēng)條件為自然通風(fēng),豎窯頂口排氣由煙囪排出。有時,由于天氣悶熱或礦石塊度過小等因素造成窯內(nèi)通風(fēng)不暢時,需要低壓送風(fēng)。
4)豎窯上部煙道廢氣溫度應(yīng)小于
5)高鋁礬土礦石理論灼減值為15%,實際灼減為30%左右。
6)物料的裝料深度為0.7~
6)每次間隔落料時間為2h~2040min。
7)每窯循環(huán)時間為60~72h。窯的容積越大,循環(huán)時間越長。
8)容積為50~
8)熟料質(zhì)量塊度3~
9)制作高鋁磚用高鋁礬土熟料的質(zhì)量要求如冶金部頒標(biāo)準(zhǔn)YB2212~82。
本文由河南耐火材料廠整理,未經(jīng)允許,不得轉(zhuǎn)載。
相關(guān)資訊
30
2024-08
27
2024-04
27
2024-04
01
2023-12
01
2023-12
01
2023-12
01
2023-12
01
2023-12
01
2023-12
01
2023-12
熱門產(chǎn)品
全國咨詢熱線
13608687008
鄭州新密市超化鎮(zhèn)工業(yè)園區(qū)
備案號:豫ICP備16041729號
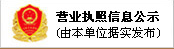